Copper Alloy Series
Description
Copper alloy casting may be influenced by some factors, such as tensile and compressive strength, wear qualities when subjected to metal-to-metal contact, machinability, thermal and electrical conductivity, appearance and corrosion resistance. These factors should take into consideration for maximizing the product performance.
The preheating temperature of the metal mold used for copper alloy casting is about 100℃. The preheating temperature can not be too high, easy to peel off. The metal mold and core must be preheated before coating, so the water evaporates quickly when painting the metal mold, it will obtain firmly bonded coating layer. Copper alloy investment casting can adopt electric heating and gas heating methods.
Application of Copper Alloy Investment Casting
Copper alloy castings can be used for applications such as bearings, bushings, gears, fittings, valve bodies, and miscellaneous components for the chemical processing industry. They are primarily used in automotive and aerospace applications.
These alloys are produced by many types of casting processes, such as sand casting, shell casting, investment casting, centrifugal casting and die casting.
Differences between Copper Alloy Casting Processes
The casting processes are different due to various crystallization characteristics of different copper alloys and casting properties.
1. Tin bronze. Its crystallization characteristics are large crystallization temperature range and wide solidification zone. Poor fluidity, the copper alloy casting is easy to produce shrinkage and easily oxidized. The thick walled castings adopt directional solidification, and complex thin-walled parts use simultaneous condensation.
2. Aluminum bronze and aluminum brass. The crystallization characteristics are small crystallization temperature range and layer by layer solidification. The casting performance has good fluidity, easy to form concentrated shrinkage and easily oxidized. The characteristics of the investment casting are as follows: aluminum bronze casting system adopts bottom pouring style, while aluminum brass uses open style.
3. Silicon brass. Its crystallization characteristics are between tin bronze and aluminum bronze. Casting performance is the best (in a special brass). Casting process is characterized by sequential solidification, gating system and blind riser is smaller.
Founded in 2010, Shanghai ZZ Group Non-Ferrous Casting Co., Ltd. is a professional manufacturer and supplier of copper alloy casting in China. We can provide sand casting, gravity casting, low-pressure casting, investment casting, aluminum alloy casting, centrifugal casting, free forging and die forging as well as precision machining. The raw materials include copper, aluminum, zinc, gray iron, ductile iron, cast steel, high temperature alloys and other materials. If you are interested in our copper alloy casting, please contact us.
Related Products
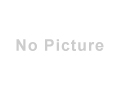
- Forging Material SeriesPrecision forging technology is a combination of hot forging and cold forging process. It permits to manufacture high-strength components with complex functional elements. They deliver a high surface quality with close dimensional tolerances....
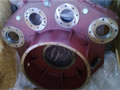
- Iron Casting SeriesIron castings are typically used for the energy (oil & gas), automotive, agriculture, valve and pump industries. As a raw material iron is much cheaper than stainless steel because of the high cost of the nickel and chrome added to steel....