Forging Process
Description
Forging process utilizes forging machine to force pressure on the metal blank in order to make it generate plastic deformation and obtain a certain mechanical properties, shape and size. Forging and stamping belong to plastic processing properties, generally called forging and pressing.
Forging process is a common forming method in mechanical manufacturing. As-cast porosity and welding holes of the metal can be eliminated by free forging. The mechanical property of forgings is generally superior to the castings with same material.
The important parts with high load or under serve working conditions are mostly made by die forging process, except the plates, profiles or welded parts with simple shapes by rolling.
Classification of Forging Process
1. According to the temperatures of the blank during the processing, it can be divided into cold forging and hot forging. Cold forging is generally processed at room temperature, while hot forging is machined at the recrystallization temperature which is higher than the billet metal. Sometimes the forging process is in a heated condition, but the temperature does not exceed the recrystallization temperature, called warm forging.
2. It can be classified into free forging, die forging, cold heading, radial forging, extrusion, roll forming, roll forging and ring rolling according to the forming methods. Billets are deformed under pressure and are not subject to external constraints, called free forging. Billets deformation via other forging processes are limited by the moulds, called closed die forging. There is a relative rotational movement between the forming tools and the billets, which presses and forms the billets point by point, this is called rotary forging.
Materials of Forging Process
Main materials are carbon steel and alloy steel, followed by aluminum, magnesium, copper, titanium and its alloys. The original state of the material includes bar, ingot, metal powder and the liquid metal.
Forging Process Flows
1. The general sequences of free forging are as follows: laying-off of forging billet, forging stock heating, roll forging standby billet, die forging forming and trimming.
2. Intermediate inspection is carried out to check the size and surface defects of the forgings.
3. The forging process uses heat treatment to remove forging stress and improve the performance of metal cutting.
4. The surface oxidation layer of free forging should be removed.
5. The appearance and hardness of common forgings should be inspected, and the important forgings should carry out chemical composition analysis, mechanical properties and residual stress testing as well as non-destructive testing.
Founded in 2010, Shanghai ZZ Group Non-Ferrous Casting Co., Ltd. specializing in research, development, production and sale of forging process, metal casting process, and precision machining. Our company has the capacities to carry out free forging, die forging, sand casting, gravity casting, low-pressure casting, centrifugal casting as well as investment casting. We have a complete quality system, excellent management and sales system. We will provide our customers with satisfactory products and services.
Related Products
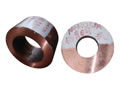
- Centrifugal CastingThe centrifugal casting is a metallurgical manufacturing process that is typically used to cast thin-walled cylinders. Unlike other non-ferrous casting, this casting process is used to produce stock materials in standard sizes for further machining, rather than shaped parts tailored to a particular end-use....
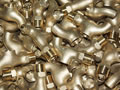
- Coated Sand CastingThe resin sand casting equipment consists of shell core machine, core shooter, casting machine, advanced coated sand formula and manufacturing technique.This sand casting process is suitable for the production of cars, tractors and hydraulic parts. The molding materials include copper, iron and steel....