Gravity Casting
Advantages of Gravity Die Casting
1. Gravity casting utilizes the force of gravity to fill a permanent mold or die with molten material. It does not use the high-pressure method to form the casting.
2. It will ensure that there will not be any clusters formed during this casting process.
3. This casting features in cost effective, good quality, and process control over other non-ferrous casting techniques.
4. Gravity casting is done in ceramic molds, permanent casting, sand casting as well as in investment or lost foam casting.
5. This gravity die casting adopts cast iron moulds which allow aluminum and zinc castings to be produced more accurately and cheaply than with sand casting.
6. The rapid cooling gives excellent mechanical properties whilst non-turbulent filling ensures production of heat treatable gravity castings with minimal porosity.
Description
Gravity casting refers to a kind of foundry technology which injects the molten metal into the metal mold under the action of gravity. The gravity die casting has wide adaptability, and it can be used in the production of various casting products. The surface roughness of this non-ferrous casting is smoother than that of the sand casting. The materials include aluminum, copper, zinc, iron and steel.
Gravity Casting Process
The mold cavity is coated with a refractory material or a mold wash, which can prevent the casting form sticking to the mold and extend the lifespan of the mold. Any sand or metal cores are installed and the mold is closed tightly. Molten metal is then poured into the mold. Soon after solidification, the mold is opened and the casting removed to reduce chances of hot tear. The gravity die casting process is then started all over again, but preheating is not required because the heat from the previous casting is sufficient and the refractory coating should last several castings. Because this gravity casting process is generally implemented on large production run of automated equipment, which is used to coat the mold, pour the metal, and remove the casting.
Process Control
Comprehensive set-up records and quality data guarantee consistent production and reduce set-up time of the gravity die casting.
Tool and Gravity Casting Design
Our experts will give you optimal design, and eliminate the elements which add unnecessary costs to your non-ferrous casting. Thus we provide the benefits of automated production of aluminum or zinc die casting without high-cost tooling.
Images Information
Material: A356-T6
Technology: Gravity casting
Application: Equipment component |
Material: ZAlZn10Si8Mg
Technology: Gravity die casting
Application: Engineering machinery |
Founded in 2010, ZZ Group Non-Ferrous Casting Co., Ltd. is a professional manufacturer and supplier of non-ferrous casting in China. We have the abilities to carry out sand casting process, gravity casting, low pressure casting, centrifugal casting, and ferrous metal casting process. In addition, we provide forging process products and precision machined products for your choice. We will provide our clients with satisfactory gravity die casting and services, and sincerely hope to establish permanent cooperation with each customer.
Related Products
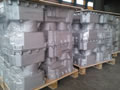
- Low Pressure CastingLow pressure casting technology is widely used for the production of engine bearer, engine manifold and gear box in the industries of vehicle, shipbuilding and locomotive. The low-pressure metal casting uses a gas at low pressure, generally between 3 and 15 psig to push the molten metal into the mold cavity. The pressure is appl...
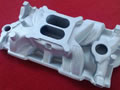
- Shell CastingShell casting puts resin coated sand on the preheated metal template with mould, makes the resin melt and form a layer of shell. It achieves the desired moisture and rigidity after melting, drying and hardening....