Shell Casting
Features of Shell Mold Casting
1. This shell casting technology can reduce the quantity of the foundry sand and obtain a clear outline, smooth surface and precise size. It does not need machining process or only a small amount of machining.
2. The shell mold casting is especially suitable for producing various alloy castings with larger batch, high dimensional accuracy and complex shapes, but the manufacturing cost is relatively higher.
3. This shell casting process can achieve fully automation for mass production.
4. The characteristics of the shell mold casting are high productivity, low labor costs and excellent surface finishes.
Description
Shell casting puts resin coated sand on the preheated metal template with mould, makes the resin melt and form a layer of shell. It achieves the desired moisture and rigidity after melting, drying and hardening.
The shell mold casting is applied to the automobile, train, shipbuilding, electronic and semiconductor industries. The material can choose a variety of copper alloys, aluminum alloy, zinc alloy, ductile iron, gray iron, stainless steel and carbon steel.
Shell casting is a metal casting process similar to sand casting, in that molten metal is poured into an expendable mold. However, in shell mold casting, the mold is a thin-walled shell created from applying a sand-resin mixture around a pattern. This casting process requires the use of a metal pattern, sand-resin mixture, dump box and molten metal.
Shell Casting Process
The shell mold casting process is composed of the following steps:
1. Patten creation
A two-piece metal pattern is set up in the shape of the desired part, typically from iron or steel. Other materials are also can be used, such as aluminum for low volume production or graphite for casting reactive materials.
2. Mold creation, mold assembly
After the molten metal is cooled, the mold can be broken and the castings can be removed. Trimming and cleaning processes should remove any excess metal from the feed system and any sand from the mold.
Images Information
Material: A356-T6
Technology: Shell casting (sand mould-resin sand)
Application: Important components of engine
Material: ZL 101A-T6
Technology: Shell mold casting (low pressure -resin sand)
Application: 110KV-550KV switch shell
Technical condition:
1. 100% hydraulic pressure 0.78x2MPa, which lasts 30 minutes without permanent deformation phenomena
2. Destruction of water pressure is more than or equal to 0.78x3.5MPa
3. Seal test, if charged 0.6MPa SF6 gas, the annual leakage rate is less than 0.5%
Material: A356-T6
Technology: Shell casting (sand mould-resin sand)
Application: Medical important parts |
Material: G-AlSi7Mgwa
Technology: Shell mold casting (low pressure -resin sand)
Application: Painting equipment |
Material: Brass
Technology: Shell casting (sand mould-coated sand)
Application: Living goods |
|
|
ZZ Group Non-Ferrous Casting Co., Ltd. is a professional shell mold casting manufacturer and supplier in China. Our company has the capacities to carry out casting process (including sand casting, gravity casting, shell casting, low-pressure casting and centrifugal casting), forging process (like free forging and die forging) as well as precision machining. Our metal casting products like shell casting process involve in many fields, such as military, high-speed rail, ship, engineering machinery, wind power, power plant and electrical equipment.
Related Products
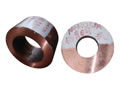
- Centrifugal CastingThe centrifugal casting is a metallurgical manufacturing process that is typically used to cast thin-walled cylinders. Unlike other non-ferrous casting, this casting process is used to produce stock materials in standard sizes for further machining, rather than shaped parts tailored to a particular end-use....
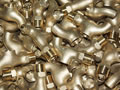
- Coated Sand CastingThe resin sand casting equipment consists of shell core machine, core shooter, casting machine, advanced coated sand formula and manufacturing technique.This sand casting process is suitable for the production of cars, tractors and hydraulic parts. The molding materials include copper, iron and steel....